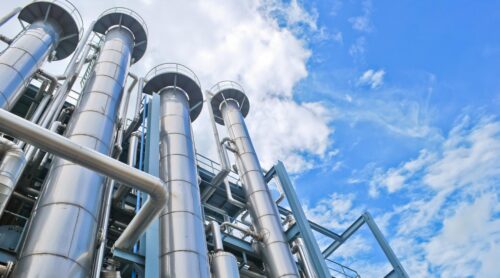
This article is part of a series. To learn more, please see our other articles in this series: Clean Energy 101: The Chemicals and Climate Connection, How Hydrogen Could Clean Up the Chemicals Industry, and From Waste to Value: How Carbon Dioxide Can Be Transformed into Modern Life’s Essential Products.
Thermal Batteries: Electrifying Heating in Chemical Plants
A guide to bringing thermal batteries to chemical and refining plants across the United States.
The heating needs of the chemicals and petroleum refining sectors account for 5 percent to 6 percent of US greenhouse gas emissions. Today, most of this heat is generated by burning natural gas or other fossil fuels. As industry faces increasing pressure to reduce emissions, thermal batteries’ potential to abate as much as 99 percent of current heat emissions when coupled with renewable energy make them an attractive alternative for industrial heating.
This guide was designed to help industry and policy stakeholders better understand where and how the chemicals and refining industries can implement thermal batteries today, and how policy can support industrial electrification.
What Are Thermal Batteries? (Heat Batteries)
Thermal batteries are made with materials that have a high capacity to absorb and store heat, such as graphite, crushed rock, and bricks. These materials are heated to temperatures up to 1800°C using electricity. The heated materials are encased in insulation to efficiently store heat for up to a few days, and release the heat as needed to industrial plants for uses such as heating for reactions, distillation, and drying.
Thermal batteries typically charge for 4 to 8 hours per day and take advantage of periods of low to negative electricity pricing during off-peak utilization of the grid, cutting charging costs by up to 50 percent. Since periods of low electricity prices tend to occur when there is a surplus of renewable energy on the grid, thermal batteries cut emissions when compared to gas-fired heating. For plants with access to off-grid renewables, either through direct ownership or through power purchase agreements (PPAs), thermal batteries provide reliability benefits by buffering the intermittency of wind and solar generation to provide steady-state heat.
Picturing a Thermal Battery in Nearly Every Chemical Plant
Thermal batteries are a versatile technology; they can be utilized in a variety of ways to reduce emissions. The main uses of heat in chemical plants are for reactions and separations.
Reactors are where chemistry happens to make the stuff we use in our everyday lives like fertilizers and the base chemicals of plastics. Often, this chemistry requires significant amounts of heat at high temperatures, as high as 1100°C, depending on the reaction. A thermal battery can pre-heat the reactants going to the reactor or directly heat the reactor.
Typically, a mixture of chemicals comes out of a reactor and needs to be separated. Distillation separates chemicals based on their boiling points, resulting in streams of more pure chemicals. In chemical plants, distillation requires heat at temperatures ranging from 100°C to 300°C. Most plants burn natural gas to heat water into steam, then pipe the steam via a vast network of pipes to the distillation columns, reactors, dryers, and myriad other users of heat in the plant. Thermal batteries can replace or supplement existing natural gas boilers, and, with thoughtful integration, they can also improve the reliability of steam supply.
Plugging a Thermal Battery into a Chemical Plant
Chemical plants can achieve significant reductions in greenhouse gas emissions, improve energy efficiency, and potentially lower energy costs by integrating thermal batteries for their heating needs.
Thermal batteries are a new application of existing, proven technologies including direct resistance heating and firebricks, and their integration into plants is straightforward and within the capabilities of the existing ecosystem of service providers involved in US industrial hubs such as engineering, procurement, and construction firms.
The integration steps would include:
- Assess and Plan: Evaluate current heating requirements, identify potential integration points, and design a system that aligns operational needs and emissions reductions goals.
- Design and Retrofit: Modify existing steam systems, furnaces, or other heaters to connect thermal batteries. This may involve installing heat exchangers and updating control systems for seamless integration.
- Automation and Control: Implement automated systems to manage the charge and discharge cycles of the thermal batteries based on electricity price signals and heat demand.
- Monitoring and Maintenance: Establish protocols for regular monitoring and maintenance to ensure optimal performance and longevity of the thermal battery system.
Getting The Investment Decision Right
Thoroughly evaluating the factors listed below will help chemical plants make informed decisions about integrating thermal batteries, maximizing both economic and environmental benefits.
- Energy Demand and Usage Patterns: Understanding the plant’s energy consumption patterns dictates the size and configuration of the thermal battery system. Plants should consider thermal batteries as elements of their long-term electrification plan, and build in flexibility to meet present and future energy flow and consumption patterns.
- Grid and Market Conditions: Local electricity prices, grid reliability, and the availability of renewable energy sources can influence the economic viability and emissions reduction potential of the project.
- Capital and Operating Costs: Evaluating the initial investment required for installation and the ongoing operational costs, including maintenance and energy costs, is crucial. Thermal battery manufacturers may offer clean heat as a service, where they operate and maintain the thermal battery and bill for the energy monthly as part of a long-term contract. Companies with capital constraints should consider this emerging energy procurement model in the industrial sector. In addition, plants must closely consider electrical infrastructure upgrades needed for their electrification plan: when planning these upgrades, they should work with local utilities to negotiate rates, cost sharing for grid upgrades, and other incentives.
- Regulatory and Policy Landscape: Understanding the regulatory environment, including tax credits, subsidies, and carbon pricing mechanisms, can impact the financial feasibility of the installation.
- Environmental Impact: Considering the co-benefits, including reduced air pollutant and greenhouse gas emissions; and improved energy efficiency, can support the decision-making process. In addition, an internal price on greenhouse gas emissions can help bolster the business case for thermal batteries.
Thermal Batteries by The Numbers
Thermal batteries are a mature technology that can supply heat at temperatures up to 1800°C with up to 99 percent emissions reduction potential over natural gas-based heating, when charged with renewable electricity. The levelized cost of heat (LCOH) delivered ranges from $20 to $87 per megawatt hour (MWh). 20 percent to 40 percent of the cost is capital expense; the remaining is operational expense, mostly of purchased electricity. Smart charging configurations, such as a two-way grid-connected thermal battery, can help chemical plants land LCOH at the lower end of the range.
When comparing thermal battery technologies, specific heat capacity (ability to store heat), thermal conductivity (ability to conduct heat), and efficiency (resistance to heat loss) are the key performance indicators to consider. Additionally, for consumers that require combined heat and power delivery, thermal battery manufacturers will differentiate themselves through their heat-to-power conversion approach. Some have chosen to design systems that can integrate existing steam turbines while others are developing conversion technology like thermophotovoltaic (TPV) panels which were previously costly and inefficient but are becoming cost competitive with leading conversion efficiencies of greater than 40 percent.
If Not a Thermal Battery, Then What?
Process heating up to 200°C, which accounts for 60 percent of heating related emissions, can be decarbonized across the United States by utilizing heat pumps. Heat pumps improve energy efficiency by upgrading and utilizing low-grade heat that would otherwise be wasted. Heat pumps can often be implemented alongside thermal batteries to maximize energy efficiency and emissions reduction. Chemical plants should evaluate both technologies and determine a configuration, whether they use one or both technologies, to suit their specific process needs.
There are fewer options for the higher temperature process heat that is typically needed for distillation and reactions. Solar thermal is one option that can decarbonize process heat from 300°C up to 1200°C depending on technology type (linear Fresnel vs heliostat towers), but cost, need for thermal storage to combat intermittency, and solar resource availability reduce its potential scalability in many scenarios. Alternative fuels like hydrogen and biomass can be used, though their higher purpose is likely as a feedstock for chemicals in a low-emissions industry future, with some exceptions where hydrogen may be used as a fuel economically and sustainably.
Policy Boost: The 45X Advanced Manufacturing Tax Credit & 48C Advanced Energy Project Credit
Thermal batteries are eligible for credits under the 45X and 48C sections of the Internal Revenue Code. This will help lower the levelized cost of heat from thermal batteries, making them a competitive source of process heat for some customers. The tax credit is available for 10 years; given long 3-to-7-year capital planning cycles and 1-to-3-year plant maintenance turnaround cycles, now is the time to evaluate this technology during your strategic planning.
Enabling Policy
State-level policies are needed to make thermal batteries competitive for more customers and in electricity markets throughout the country:
- Wholesale Electricity Rate Access: Allow thermal batteries to access wholesale rates so they can utilize excess renewables that would otherwise be curtailed during off-peak hours. For customers, it will reduce operating costs. For the grid, it will improve efficiency and reliability.
- Non-Adjacent Parcel Permitting Reform: Allow private distribution lines and PPA’s across non-adjacent parcels. Existing local and state rules sometimes guarantee utilities a monopoly on transmitting power across public rights-of-way, preventing commercial sale of power across non-adjacent parcels of land. This hampers industry’s ability to build dedicated renewables close to their plants. Since most industrial plants are not situated on sufficiently large, uninterrupted parcels of land to build the generation capacity they need, this limits their potential to electrify operations. Co-locating flexible loads like thermal batteries with renewables and other commercial and industrial plants means lower individual investment costs, strategic charging times that can further cut electricity costs to end users, and peak-load support for the grid.
- Grid Enhancing Technologies (GETs), Transmission, and Interconnection Queue Resolutions: Transmission and interconnection queue reform can facilitate faster integration of new clean generation onto the grid ensuring a reliable and reachable supply of clean energy for thermal batteries. This also helps free up transmission carrying capacity where new transmission might not be built fast enough to meet increasing industrial demand.
- Industrial and Trade Policies: Providing subsidies for low-carbon industrial products, or for clean industrial process heat production, and implementing carbon pricing on high-emission products creates a financial incentive for industries to adopt thermal batteries and other electrified solutions, driving broader market adoption. Implementing three-pillar rules (additionality, hourly-matching, and regionality) to these electrification technologies would be crucial to ensuring those processes or products’ low emissions profile, while accelerating grid decarbonization and resilience.
Seizing the Opportunity
Thermal batteries have the potential to serve as the foundation of reliable low emissions electrified heat in chemical and refining plants across the country. By leveraging existing policy incentives and advocating for new supportive measures, we can unlock the full potential of thermal batteries, driving significant emissions reduction toward a climate-aligned chemicals industry.