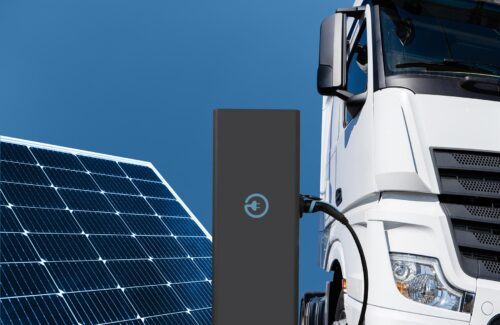
How Electric Truck Fleets Can Save Money with Smarter Charging, Solar Power, and Batteries
Managed charging and distributed energy resources can save fleets up to 30 percent in electricity bills while reducing the time and costs associated with grid connections.
The electric revolution in trucking is picking up speed. Deployment of electric medium- and heavy-duty vehicles (MDHD) jumped 44 percent from 2023 to 2024. Adoption of zero-emissions vehicles is particularly high in California, which has strong vehicle incentives and policies like the Advanced Clean Truck Rule. Since its passage in 2021, the state has seen remarkable progress. In 2023 alone, more than 18,000 medium- and heavy-duty vehicles were sold in California, with zero-emissions trucks making up one in six fleet vehicle sales.
California’s leadership in decarbonizing heavy transport is one of the reasons the region was selected for RMI and Mission Possible Partnership’s (MPP) work on clean industrial hubs in partnership with the Bezos Earth Fund. Favorable subnational policy and rising demand for lower-emissions supply chains have been fueling progress statewide, but there is more work to be done to accelerate adoption and lay the groundwork for uptake across the United States.
While electric trucks (e-trucks) are rapidly gaining market share, they are still a minority of sales and significant challenges remain. One key challenge is optimizing charging to meet fleet operational needs while minimizing fuel costs. To address this challenge, the RMI and MPP team analyzed electricity rates from the Los Angeles Department of Water and Power (LADWP) to better understand how fleets can charge their e-trucks affordably.
We found that managed charging — an operational strategy that prioritizes charging during off-peak hours — and distributed energy resources (DERs) like solar panels and battery storage can greatly reduce charging costs while also serving as a stop gap charging solution as fleets work on deploying electric depots, which can take years. While we found that charging during off-peak hours yields the most significant savings, deploying DERs can also reduce costs considerably.
Below, we discuss the advantages of managed charging and DERs and barriers to their implementation.
Managed charging saves money
Although unmanaged charging saves fleets money when compared to diesel and gasoline trucks, managed charging can save even more, helping defray the higher up-front cost of e-trucks.
We found that by charging during off-peak hours, fleets can save up to 30 percent in charging costs.
This strategy would reduce the cost per mile from 36¢ to 26¢ for a heavy-duty truck, far undercutting the 70¢ per mile of a diesel equivalent. Given that managed charging requires no charger upgrades or new installations, and therefore no up-front capital costs, fleets have much to gain by adopting this flexible approach.
Fleets that use managed charging often charge overnight, when electricity demand is low. Many also use lower-power chargers, a practice known as slow charging. While overnight charging has lower electricity costs than slow charging, fleets that charge for many hours at as low a power level as possible also generate significant cost savings, as much as 20 percent. Slow charging also reduces a depot’s peak load by as much as a third, compared to off-peak overnight charging that can require a 10 percent larger interconnection. Charging at the right speed not only lowers ongoing electricity costs, but can also help avoid overspending on chargers or utility upgrades.
Challenges to implementing managed charging
Managed charging can be difficult to implement, as it requires experience to successfully implement. For example, one southern California fleet reduced its peak load by 1 MW through managed charging. However, the fleet only realized these savings after a year of optimization. They are now saving money on their ongoing electricity bills, but they paid for an over-sized grid connection they no longer use.
While there are software solutions that can make managed charging easier to deploy, to most effectively manage charging, fleets need knowledgeable on-site staff who can move vehicles to chargers overnight. Additionally, although software solutions are affordable to implement, they can also be rigid: for instance, a late-returning vehicle or unplugged vehicle can cause higher electricity costs or operational failures. Fleets without predictably fixed routes will need to be mindful of these constraints as their operations require flexibility.
Adding solar and batteries saves time and money
While managed charging is a powerful way to reduce costs, it can be difficult to implement and, as we note above, operationally rigid. DERs in the form of solar energy and battery storage can save fleets money either with managed charging or as a standalone strategy.
In California, solar energy is abundant, and solar panels are now extremely cheap, with prices around $1.5 per watt after incentives for commercial systems up to 1 MW, providing substantially cheaper daytime energy than the grid. For a depot with sufficient roof or canopy space, maximizing solar capacity is a no-regrets action that can save significant money for fleets that charge during the daytime, and even save money for overnight charging cases, with or without net metering, when partnered with battery storage. And solar panels can power a portion of a fleets' vehicles during the day, with excess energy fed back into the grid or stored in batteries for overnight use.
In fact, if space allows, on-site solar and battery storage can produce nearly the same electricity cost savings as managed charging, though this is offset by increased capital costs. As an additional benefit DERs can even reduce a site's overall interconnection size and energy draw from the grid. In Southern California, for instance, adding DERs can reduce the lifetime costs of a truck facility by 5–10 percent if utility rates allow net metering and incentivize demand load shifting, with the greatest savings accruing for e-trucks that are unable to charge during off-peak hours.
On-site batteries can also provide fleets with more flexibility, especially for those who are unable to implement managed charging. Batteries store energy, and they can discharge this energy when vehicles need to charge during peak periods or blackouts. For example, a flat tire or an unexpected delivery could mean that an e-truck has to charge during peak hours, costing a fleet $500 or more in additional demand charges and raising overall annual electricity costs by as much as 40 percent. On-site batteries can be charged during off-peak hours when there is spare capacity and can then be used to charge vehicles during expensive peak hours.
Barriers to implementing DERs
Adding distributed energy to a site can improve a fleet’s economics and flexibility and avoid grid upgrade costs that can impact all customers, but current utility and regulatory processes can delay connecting the site to the grid. So, while DERs should help avoid time-consuming grid upgrades, fleets and developers sometimes shy away from them because engineering and permitting processes can increase the time it takes to get a grid connection. And, under some utility programs, incorporating DERs can remove EV charging discounts from electricity bills. These DER disincentives harm EV fleets and utilities that are struggling to meet new demand. These barriers are particularly troubling because managed charging and inclusion of DERs can help avoid some distribution upgrades, which are expected to cost California ratepayers as much as $50 billion by 2035. Thankfully, many utilities now encourage customers to use batteries and more need to follow suit by streamlining their processes.
The barriers to DERs are not just related to the grid. Permitting requirements can be complex and time-consuming for DERs, with fire safety regulations around battery storage in Los Angeles County being particularly strict.
High upfront costs are another substantial barrier. Purchasing electric trucks and chargers often costs above $400,000 per truck and $100,000 per high-capacity charger. Adding investments of $1 million or more to add large solar and storage to the site, which may take 5–8 years to pay back, may be difficult for some fleets. Physical space is also a major restriction for many existing depots built solely for parking vehicles, with most of the DER-heavy sites open today being bespoke facilities.
Don’t Discount Utility Rates The cost of electricity varies significantly by utility and in multi-faceted ways. Electricity costs vary by time of day, monthly peak demand charges, up-front interconnection fees, potential solar and battery revenue, and the division between monthly connection size used (MW) and energy (MWh).
All other things being equal, the best charging plan depends on utility rate structure, which is why it’s critical that stakeholders understand these rates. Utilities set their most expensive peak pricing times at different times of day, which means that fleets will have to adjust their operations to save the most money. For example, on a summer weekday, LADWP’s and neighboring Southern California Edison’s peak charging rates occur at different times in the day. This incentivizes different optimal charging and DER strategies.
DERs generate more annual savings where fleets are unable to charge off-peak in LADWP territory. These trends apply to other utilities that have a peak and off-peak demand charge difference and are compounded where there is less than full retail solar net metering.
Note: Electricity costs used include all rate components for LADWP large commercial service including time-of-use rates and demand charges, vehicle mileage, and possible charging patterns from analysis of Geotab telematic data for fleet vehicles in Los Angeles.
What fleets and utilities can do to accelerate the use of managed charging and DERs
Fleets should:
- Incorporate the maximum amount of managed charging that is viable and assess the potential value of DERs from the get-go. As a first step, fleets should understand their electricity needs using vehicle telematics prior to commencing electrification and then look at the costs of these loads under their utility tariffs.
- Use tools such as NREL’s ReOpt to understand how DERs can reduce loads and costs.
- Work with a charging partner to ensure a right-sized and optimized system. Bringing a charging partner in early in the site operation design process will save fleets significant time and money in the long run, as permits to add batteries after the charging installation and upgrades can sometimes take several years.
Utilities should:
- Leverage DERs and managed charging to get more customers online, which will defer the need for upgrades and act as a potential downward pressure on rates.
- Incentivize DER installation and managed charging, both through financial incentives such as expanded make-ready programs and through optimized time-of-use rates.
Together these factors can help accelerate medium- and heavy-duty truck electrification and help fleets meet Advanced Clean Trucks requirements, while using rate payers’ money more efficiently for everyone.
While there are barriers to managed charging and DER implementation, RMI and others’ research shows that the significant cost and time savings justify efforts to streamline their deployment.
About Clean Industrial Hubs
The insights discussed above come from RMI and the Mission Possible Partnership’s (MPP’s) Clean Industrial Hub in Los Angeles, California, which accelerates industrial and heavy transportation decarbonization in the region. Clean industrial hubs bring together policymakers, financial institutions, project developers, and community-based organizations to enable groundbreaking decarbonization projects in the hardest-to-abate sectors. In Los Angeles, RMI and MPP’s analyses, convenings, and tools support stakeholders working to advance zero-emissions trucking, low-carbon cement plants, sustainable aviation fuel, and decarbonized ports by increasing the size, scale, and speed of critical climate investments that benefit the environment, the economy, and communities. This work is done in partnership with the Bezos Earth Fund.
Methodology
As part of a previous article, RMI produced load curves for managed and unmanaged charging in Los Angeles based on telematic data of real fleets. In this analysis we have scaled these up to model the load curve for a single representative MHDEV depot of around 100 vehicles and then applied LADWP A-3 large commercial rates. Our DER analysis was done in part using NREL’s ReOpt tool, an online model that allows users to input their current load profiles, select the rate they are on, and then assess the economic savings and resilience benefits that can be obtained by integrating DERs into their site. We then supplemented this analysis by interviewing fleets, charging station operators, and DER providers who operate across Southern California.